Energy
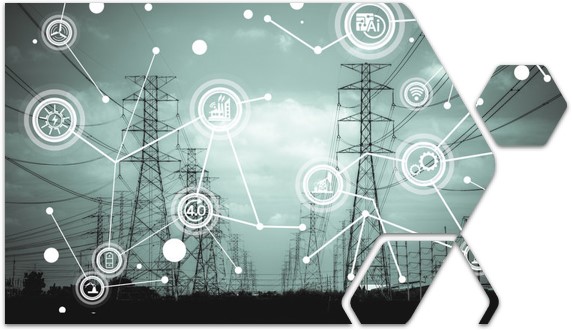
Energy
Because the Artesis system is simple to install and requires little user intervention in operation, it combines low start-up costs with the significant benefits of predictive maintenance. Since it doesn’t require any sensor installation on the equipment itself, and it can be installed in non-EX areas or away of protected areas, Artesis eMCM is a particularly good solution for inaccessible equipment in the energy industry. It is the only viable solution for nuclear applications as it is installed in motor control cabinets which is outside the hazardous areas.
Service Details
Typical applications where you can monitor either electrical, mechanical and water pumping conditions:
In addition, the entire process requires a series of machines such as alternators, pumps and fans for cooling processes, among others. Artesis MCM and PCM units allow to monitor the condition of all of them in a convenient way and at a fraction of the cost of traditional condition monitoring.
Also, pumping systems are used to pump water back to the reservoir with the purpose to reuse it and cover peak demand periods. Monitor turbine, alternators and generators, as well as “pumped storage” systems with Artesis technology to ensure their mechanical and electric performance, making the right decisions for appropriate intervention according to the severity of the problem, thus avoiding failure.
Project Mission
With Artesis monitoring units, not only the turbines and generators can be monitored, but also any other motor-driven equipment, such as pumps and fans used in the cooling systems, pumps used in pressurized water reactors, condensate pumps in the main condenser, water feeding pumps in the heat exchangers, among others.
CASE STUDIES
Feed Water Pump Bearing Fault Detection
This case is from a power generation corporation, where numerous MCMs monitor critical equipment of theirs including a feedwater pump.
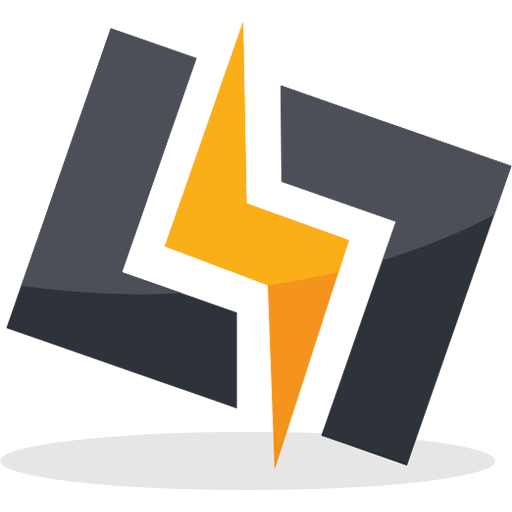
Contact Us Now for a Free Consultation
Comprehensive Condition Monitoring made easy!