Metal
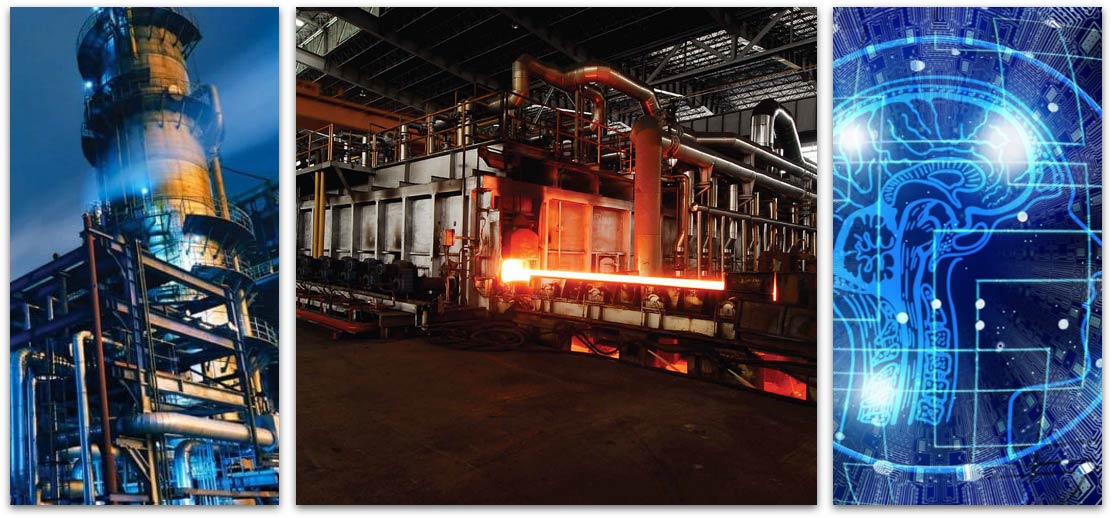
Energy
Because the Artesis system is simple to install and requires little user intervention in operation, it combines low start-up costs with the significant benefits of predictive maintenance. Since it doesn’t require any sensor installation on the equipment itself, and it can be installed in non-EX areas, Artesis eMCM is a particularly good solution for inaccessible equipment in the metal industry.
Service Details
Typical applications where you can monitor either electrical, mechanical and process conditions:
Artesis technology monitors process gas compressors, inert gas compressors, the power stack fan and the blowers. The condition monitoring is performed continuously and both mechanically and electrically speaking, helping to ensure there are no inner components failures due to misalignment, imbalance or loop wear (among others), and/or any load fluctuations due to any other external factors such as gas leakage.
Other Applications
In any metal production facility, there is service equipment that needs to be monitored. Artesis technology allows to monitor this equipment without the need of reaching them to install any kind of sensors. Monitor cooling towers, air compressors and water treatment pumps.
In addition, the metal industry also involves other production methods, such as injection molding and machining. All of them involve moving parts and rotating equipment that need to be monitored, including machine tools and conveying systems. Make sure to use the best monitoring system.
CASE STUDIES
Dirty Filter Problem of a Rolling Mill Fume Fan
This section elaborates on the details of a plugged filter detection by the Artesis early warning system at a steel manufacturing plant. The equipment monitored by the MCM is a rolling mill fume fan which discharges dust-laden air out of the factory via a filter.
The examination of the motor current trend shows that the motor current had been gradually decreasing since 17th November. This indicates that the filter blockage started on that date and had been gradually deteriorating to the point where it exceeded the MCM alarm level on 15th April.
That drop off in current shows that the fan had not been extracting the desired volume of air, and hence the ventilation in the plant would be below design levels.
The team changed the filter completely on 20th August. After that, MCM stopped giving alert signals and the motor current reverted to its nominal value.
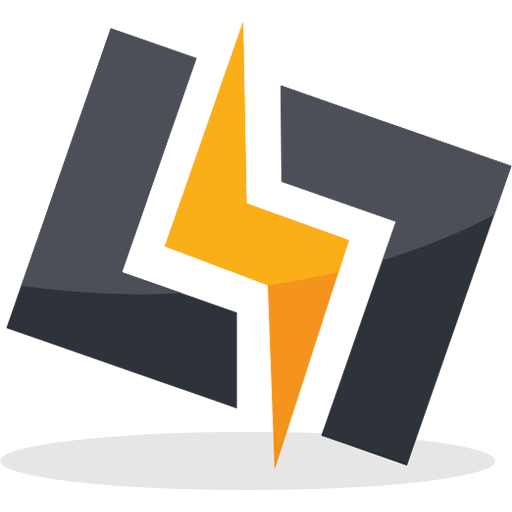
Contact Us Now for a Free Consultation
Comprehensive Condition Monitoring made easy!